Understanding the Importance of Oven Coating in the Automotive Industry
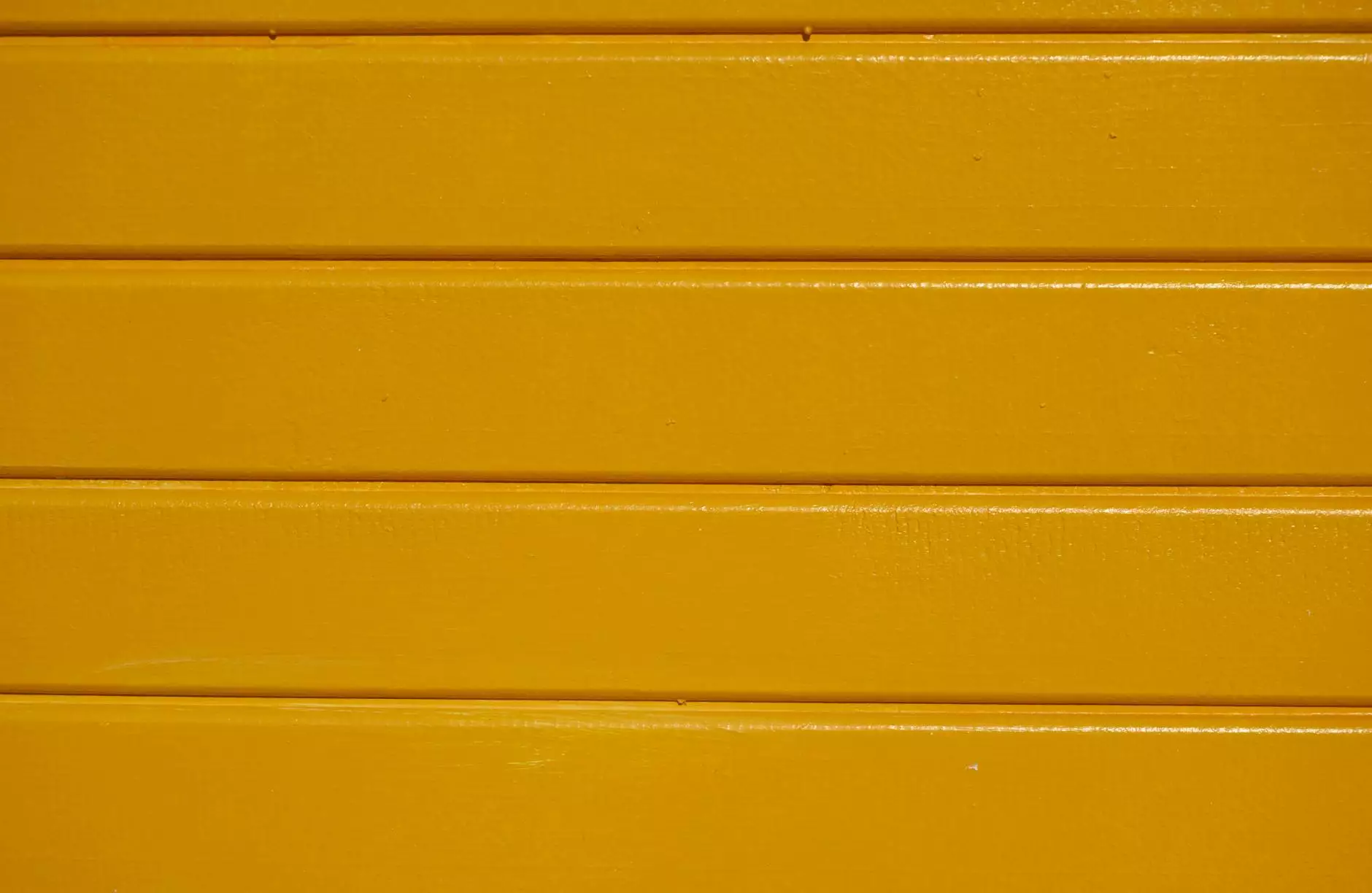
The automotive industry has been evolving dramatically, demanding innovations that enhance durability, performance, and aesthetic appeal. One such innovation that stands out is oven coating, a technique that has transformed the way automotive components are protected and presented. This comprehensive guide delves into what oven coating is, its benefits, applications, and why it is a pivotal choice for businesses, especially in the automotive sector.
What is Oven Coating?
Oven coating refers to the process of applying a protective layer to metal surfaces through a heating mechanism. This method typically involves the following steps:
- Preparation of the surface (cleaning and priming).
- Application of a powder or liquid coating.
- Heating the coated item in an oven at high temperatures.
The heating process causes the coating to cure and adhere tightly to the surface, resulting in a durable finish. This technique is particularly popular in automotive applications where long-lasting protection is essential.
Benefits of Oven Coating
Implementing oven coating in automotive production comes with numerous advantages:
- Enhanced Durability: The heat curing process significantly increases the strength of the coating, making it resistant to chipping, scratching, and tarnishing.
- Corrosion Resistance: Components treated with oven coating have increased protection against environmental factors such as moisture, salt, and UV exposure.
- Aesthetic Finish:Oven coating allows for a variety of color options and finishes, enhancing the visual appeal of automotive parts.
- Environmentally Friendly: Many oven coatings are solvent-free and emit low levels of VOCs (volatile organic compounds), making them safer for both workers and the environment.
- Cost-Effectiveness: The long-lasting nature of oven coatings reduces the frequency of re-coating, ultimately saving costs associated with maintenance and repairs.
Applications of Oven Coating in Automotive
In the automotive industry, oven coating is used across a range of applications:
- Chassis Components: Critical parts like frames and brackets often undergo oven coating to ensure strength and resilience against wear.
- Body Panels: Panels that require both durability and a visually appealing finish benefit immensely from oven coating.
- Engine Components: Engine parts are exposed to high temperatures and environments; oven coating offers necessary protection and performance enhancement.
- Wheels and Rims: The aesthetic enhancement and protection provided by oven coatings make them an ideal choice for wheels, which are often subjected to harsh conditions.
Choosing the Right Oven Coating Provider
When selecting a provider for oven coating, it's crucial to consider several factors:
- Experience: Look for companies with a proven track record in the automotive industry, such as AutoCoat India.
- Quality Primers and Coatings: Ensure they use high-grade materials to guarantee the best results.
- Technological Advancement: Providers who invest in the latest technology can offer superior coating solutions.
- Testing and Quality Assurance: The right partner will have rigorous testing procedures to ensure the performance and reliability of their coatings.
The Process of Oven Coating in Detail
The process of oven coating involves various critical stages:
1. Surface Preparation
Before any coating can be applied, the surface must be properly prepared to ensure optimal adhesion. This includes:
- Cleaning: Remove dirt, oils, and contaminants from the surface.
- Priming: Apply a primer that will enhance the bonding of the coating.
2. Coating Application
The selected coating, either in powder or liquid form, is then applied evenly over the prepared surface. Methods of application can include:
- Electrostatic Spray: This method charges the coating particles, allowing them to adhere uniformly to the surface.
- Dipping: The item is submerged in the coating to ensure complete coverage.
3. Curing Process
The coated item is then placed in an oven, where heat is applied. This stage is crucial as it causes the coating to cure, resulting in:
- Cross-Linking: The heat facilitates a chemical reaction that hardens the coating.
- Adhesion Formation: Proper heating ensures the coating bonds effectively to the substrate.
Environmental Benefits of Oven Coating
In today's eco-conscious market, the environmental impact of production processes is under scrutiny. Oven coating offers several environmental advantages:
- Reduced Waste: The durability of oven coatings means fewer materials are required for repairs and replacements.
- Recyclability: Many coatings can be recycled or safely disposed of, reducing landfill waste.
- Lower Emissions: The use of water-based and powder coatings significantly decreases harmful emissions compared to traditional solvent-based coatings.
Challenges and Considerations in Oven Coating
Despite the many advantages, there are challenges in the oven coating process to be aware of:
- Temperature Sensitivity: Certain substrates may be sensitive to high temperatures, requiring special consideration during the curing process.
- Color Matching: Achieving exactly the desired shade can be tricky and may require experienced professionals.
- Equipment Costs: While the long-term cost benefits are significant, the initial investment in quality oven coating equipment can be high.
Future Trends in Oven Coating Technology
As the industry moves forward, innovations in oven coating technology are anticipated to enhance efficiency:
- Smart Coatings: Development of intelligent coatings that can change properties in response to environmental factors.
- Nanotechnology: Increased use of nanomaterials for coatings that offer even more significant strength and protection.
- Automated Processes: The rise of automation in the coating process is expected to reduce labor costs and improve consistency in quality.
Conclusion
In conclusion, oven coating is a vital technology in the automotive industry, providing exceptional durability, aesthetic options, and environmental benefits. As businesses like AutoCoat India continue to innovate, the relevance and application of oven coating will only expand, leading to better products and more sustainable practices. This comprehensive insight into oven coating shows the transformative power it holds for automotive manufacturers and service providers alike.