Understanding Tool and Die Casting: A Comprehensive Guide
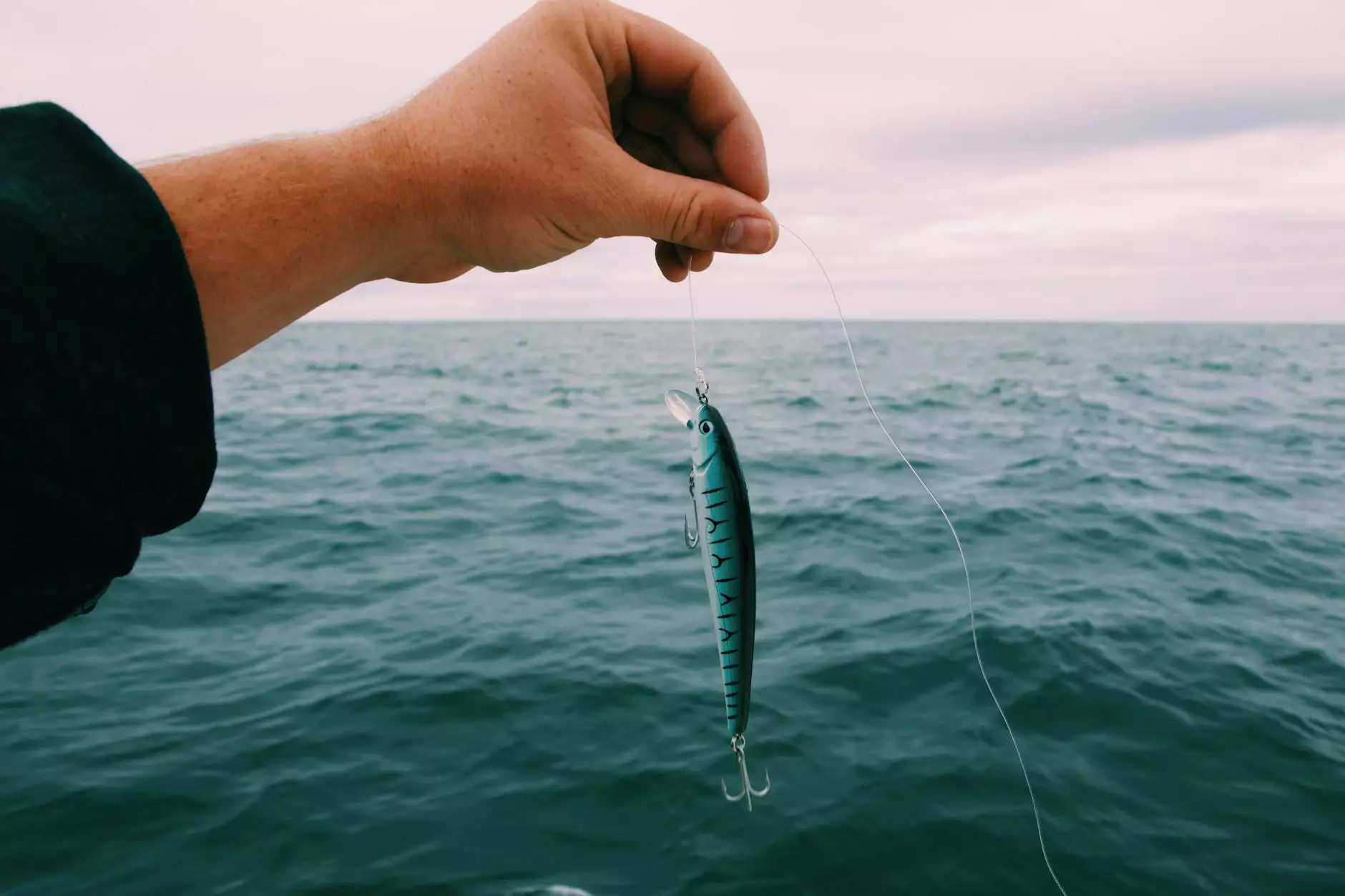
What is Tool and Die Casting?
Tool and die casting is a pivotal component of the metal fabrication sector, primarily used to manufacture components with high precision. This process entails creating a mold, also known as a die, which shapes the molten metal into desired forms. The molds are made from strong materials capable of withstanding high temperatures, ensuring high durability and repeatability in production.
The Importance of Tool and Die Casting in Metal Fabrication
In the realm of metal fabricators, tool and die casting plays a crucial role in producing intricate and reliable metal parts. It is widely utilized in various industries, including automotive, aerospace, and consumer electronics. The reasons for its significance include:
- High precision and accuracy: The process allows for tight tolerances, ensuring that parts fit together perfectly.
- Cost-effective production: Once the mold is created, mass production can take place at a low cost per unit.
- Material efficiency: Minimizing waste is a major advantage, as excess material can often be reused.
- Versatility: Tool and die casting can accommodate a wide variety of metals and alloys, expanding the possibilities for manufacturers.
The Tool and Die Casting Process Explained
The process of tool and die casting can be broken down into several key steps:
1. Design Phase
The initial stage involves designing a part and creating a detailed specification that outlines dimensions and performance requirements. This is crucial for the subsequent design of the mold.
2. Mold Creation
Once the design is finalized, a mold is manufactured from hard steel or other durable materials. This mold is precisely machined to maintain the exact geometry required for the final product. The quality of the mold directly influences the quality of the casting.
3. Melting the Metal
In the next step, the appropriate metal or alloy is melted in a furnace. The temperature must be carefully controlled to ensure optimal properties in the finished product.
4. Pouring the Metal into the Mold
The molten metal is then poured into the mold cavity. It is essential to pour the metal quickly and efficiently to avoid premature solidification and ensure a smooth flow.
5. Cooling and Solidification
After the molten metal has been poured, it must cool and solidify within the mold. This can take several minutes, depending on the material and the size of the casting.
6. Mold Removal
Once the metal has cooled, the mold is opened and the finished part is removed. This step requires care to avoid damaging the newly formed component.
7. Finishing Processes
After casting, several finishing processes may be required. This can include machining, polishing, and coating to achieve the desired surface finish and properties.
Advantages of Tool and Die Casting
Utilizing tool and die casting offers numerous advantages for manufacturers. Some of the most notable benefits include:
- Enhanced durability: Cast parts are typically stronger and more resilient than parts produced through other methods.
- Lower production costs: The ability to produce high volumes of parts efficiently helps reduce overall costs.
- Reduced time to market: Faster production times mean that companies can bring products to market more quickly.
- Improved surface finishes: The process often results in cleaner surfaces, reducing the need for additional machining.
Applications of Tool and Die Casting
Many industries rely heavily on the capabilities of tool and die casting. Here are some prominent applications:
1. Automotive Industry
In the automotive sector, this process is used to produce engine blocks, transmission housings, and various other components that require high strength and durability.
2. Aerospace
The aerospace industry utilizes tool and die casting for parts that encounter extreme conditions, making reliability a top priority.
3. Consumer Electronics
Manufacturers of electronics rely on precision casting for cases and frameworks that protect internal components while providing a sleek aesthetic.
4. Industrial Equipment
Heavy machinery and industrial equipment often require robust components that can withstand wear and tear, which is achievable through die casting.
Challenges in Tool and Die Casting
While there are numerous advantages to tool and die casting, some challenges must be acknowledged:
- High initial costs: The design and creation of molds can be expensive, which may deter smaller manufacturers.
- Material limitations: Not all metals can be effectively used for die casting.
- Complexity of mold design: Designing molds for complex parts can be time-consuming and requires specialized expertise.
Recent Innovations in Tool and Die Casting
The industry is continuously evolving, with recent innovations aimed at improving efficiency and sustainability:
1. Advanced Materials
New alloys and metal formulations have emerged, allowing for improved performance characteristics in cast parts.
2. Automation and Robotics
Utilizing automation in the casting process helps increase production speed and consistency while reducing labor costs.
3. Environmental Sustainability
Efforts to reduce the environmental impact of tool and die casting include recycling scrap metal and using energy-efficient furnaces.
Conclusion
Tool and die casting is an essential process within the metal fabrication industry, offering numerous benefits such as high precision, cost-effectiveness, and versatility. As technology continues to advance, the potential for enhanced applications of this manufacturing technique is limitless. Companies that embrace the efficiencies and innovations of tool and die casting are poised to gain a competitive edge in the rapidly evolving marketplace.
For more insights on how tool and die casting can benefit your business, visit deepmould.net and explore our extensive resources tailored for metal fabricators.