Understanding Vacuum System Components for Enhanced Efficiency
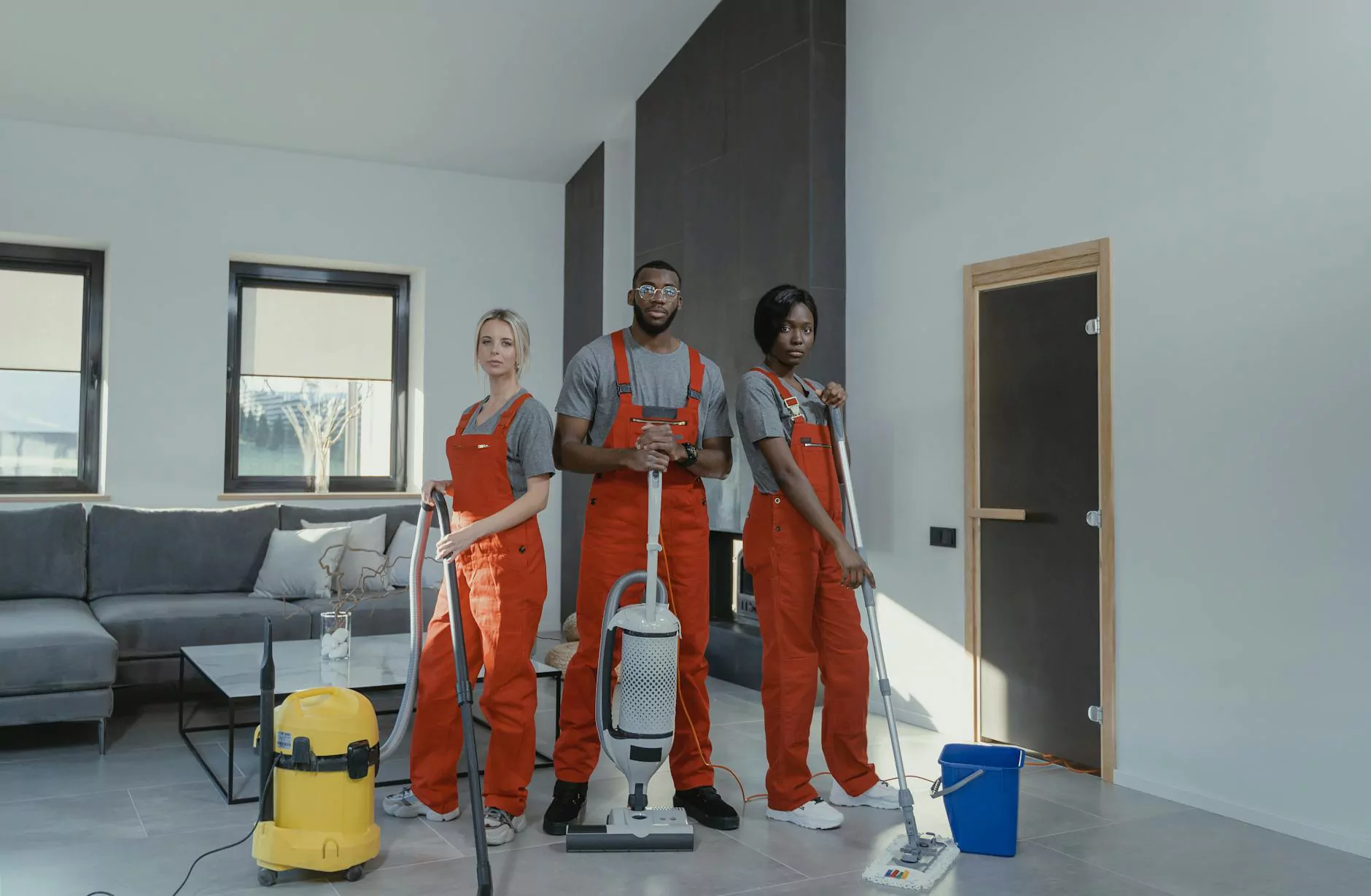
The world of industrial applications often demands precision, efficiency, and reliability. In this context, vacuum system components play a pivotal role in achieving these objectives. These systems are indispensable in a multitude of sectors, ranging from manufacturing to healthcare. By understanding their components, functionalities, and applications, businesses can optimize their operations and enhance productivity.
What are Vacuum System Components?
Vacuum system components are the building blocks that enable the creation of a vacuum — a space devoid of matter. These components work in unison to maintain and control vacuum levels, ensuring that processes proceed without interruption due to contamination, air leakage, or other factors that could compromise the integrity of the operations. The principal components of a vacuum system include:
- Vacuum Pumps
- Vacuum Gauges
- Valves
- Piping and Fittings
- Reservoirs
1. Vacuum Pumps
At the core of any vacuum system is the vacuum pump. These devices are responsible for removing gas from the designated area and creating a vacuum. They are available in various types, each tailored for specific applications:
- Rotary Vane Pumps: Known for their efficiency and durability, these pumps are widely used for medium vacuum applications.
- Diaphragm Pumps: Ideal for corrosive and hazardous gases, they provide a leak-free operation.
- Scroll Pumps: Characterized by low vibration and noise, these pumps are excellent for high-purity applications.
- Turbo Molecular Pumps: These are essential for ultra-high vacuum conditions, often deployed in semiconductor and research environments.
2. Vacuum Gauges
To monitor the vacuum level within a system, vacuum gauges are employed. These instruments provide critical feedback regarding the pressure conditions inside the vacuum chamber. Common types of gauges include:
- Bourdon Tube Gauges: These are mechanical gauges suitable for measuring rough vacuum levels.
- Pirani Gauges: Utilizing thermal conductivity, these gauges are ideal for measuring medium to high vacuum levels.
- Capacitance Diaphragm Gauges: Excellent for precise measurement in ultra-high vacuum systems.
3. Valves
Valves are critical in controlling the flow of gas and maintaining the integrity of the vacuum environment. They can be categorized into:
- Isolation Valves: Used to maintain the vacuum by isolating different sections of the system.
- Throttle Valves: These control the gas flow, allowing for adjustments in vacuum levels.
- Pneumatic Valves: Useful for automated systems, allowing for remote control of vacuum processes.
4. Piping and Fittings
The design and integrity of the piping and fittings in a vacuum system are crucial. High-quality materials are essential to minimize leaks and ensure durability. Common options include:
- Stainless Steel: Resistant to corrosion and easy to clean.
- Glass: Offers visibility for monitoring processes.
- Teflon: Ideal for chemically aggressive applications.
5. Reservoirs
Reservoirs can store the fluids or materials involved in vacuum processes, helping to ensure smooth and continuous operation. Proper sizing and material choice for reservoirs are vital to accommodate for changes in pressure and other operational needs.
The Crucial Role of Vacuum System Components in Industrial Applications
Understanding vacuum system components is not just about knowing their functionality; it's about recognizing their significance in various industries and applications. Let's delve deeper into how these components impact different sectors.
1. Manufacturing
In the manufacturing sector, vacuum systems are essential for processes such as:
- Material Handling: Vacuum systems are used for lifting and transporting materials efficiently without physical contact.
- Packaging: Vacuum packing preserves product quality and extends shelf life.
- Coating: Vacuum systems are critical in processes like vapor deposition for coating surfaces with thin films.
2. Semiconductor Fabrication
The semiconductor industry relies heavily on vacuum system components to create controlled environments for manufacturing chips. These components help maintain the ultrahigh vacuum required for processes such as:
- Etching: Removing layers from the wafer to create circuit patterns.
- Deposition: Applying thin films of materials onto substrates.
- Ion Implantation: Altering the electrical properties of semiconductors by bombarding them with ions.
3. Pharmaceuticals
In the pharmaceutical industry, maintaining sterile environments is paramount. Vacuum system components are critical in:
- Lyophilization: A freeze-drying process that preserves sensitive compounds.
- Filtration: Ensuring the purity of products by removing contaminants under vacuum conditions.
- Packaging: Vacuum sealing of medications to prevent degradation.
4. Food Processing
Vacuum systems play a vital role in food processing, especially in:
- Vacuum Sealing: Extending the shelf life of food products while preserving freshness.
- Dehydration: Removing moisture from food products efficiently under low temperature conditions.
- Cooking: Sous-vide cookery uses vacuum-sealed bags to ensure even cooking.
Best Practices for Maintaining Vacuum System Components
To ensure optimal performance and longevity of vacuum system components, regular maintenance and adherence to best practices are crucial. Here are some key actions to take:
- Regular Inspections: Inspect components regularly for wear and tear, leaks, or damage.
- Proper Cleaning: Clean components as needed to prevent contamination and maintain efficiency.
- Routine Calibration: Calibrate gauges and sensors to ensure accurate measurements are being taken.
- Keep Spare Parts: Maintain an inventory of critical spare parts to minimize downtime in case of failures.
- Training Personnel: Ensure that personnel are trained in the operation and maintenance of vacuum systems.
Conclusion: The Importance of Understanding Vacuum System Components
In summary, the knowledge and effective utilization of vacuum system components are crucial for enhancing productivity and efficiency across various industries. Their applications are far-reaching, from critical manufacturing processes to healthcare advances. By investing in high-quality components and adhering to best practices for maintenance, businesses can optimize their vacuum systems, ensuring they remain competitive and capable of meeting rising industry demands.
For businesses seeking exceptional outcomes in their operations, understanding the intricacies of vacuum systems is a step in the right direction. As industries continue to evolve, so will the technologies surrounding vacuum systems—keeping pace with innovation will be key to future success.